Materials of the future: could nature provide the solution?
Replacing plastic with biobased packaging is not an easy task, with issues such as real carbon impact, product preservation and recyclability. We get the inside story from Denis Paccaud, Innovation Director and beauty packaging specialist for Texen, and Eric Desnoes, Researcher at Innofibre, the Cellulosic Product Innovation Center.
They can be used to make delicious stews, and veggie burgers. They even perform the role of a carbon wood-wide-web in forests, and are used in the materials of certain clothes. Mushrooms are now attracting the attention of the packaging sector, in an effort to move away from petroleum-based materials. Hence why, IKEA has announced plans to replace its polystyrene packaging with a material made from mycelium (otherwise known as mushroom spawn). In Ukraine, two biochemists have designed a biodegradable material made from mushroom fibers. And in France, researchers at INRAE have developed a natural, biodegradable rubber made from tomato skins, thus repurposing an agricultural waste product.
“The industry is looking into these new materials, which could help combat the problem of the so-called sixth continent [the Great Pacific Garbage Patch],”
Otherwise said, plastic isn’t so “fantastic” when not recycled >. It has a very long life cycle of up to 500 years, and is produced in large quantities, reaching 460 million tons according to a February 2022 report by the Organization for Economic Co-operation and Development (OECD). Subject to increasingly tight restrictions (the 3R strategy), it is now believed that use of this material, if not dispensed of completely, must be reduced at all costs. Plastic is dead, long live mycelium and tomato waste products? Unfortunately, it’s not quite that simple.
Primary packaging for cosmetics and food products is subject to clear preservation and health regulations. “These restrictions stipulate that [these new materials] must at least be suitable for food contact and have no effect on the contents,” adds Denis Paccaud. At present, there are no packaging solutions that would render plastic completely obsolete. Consequently, primary packaging made from molded pulp (paper), mycelium or agricultural residues, designed to come into direct or indirect contact with products, must incorporate a barrier, which is currently still made of plastic.
“And the thinner this layer, the more effective it must be in protecting the contents from oxygen, water vapor, UV rays, etc. This is a matter of considerable debate at the moment, with PFASs being most commonly used”
PFASs are per-or poly-fluorinated substances, which because of their long life cycle, are known as forever chemicals, and whose toxicity, in some cases, was criticized last August in a study produced by the NGO Générations Futures.
These polymers are used to coat certain types of cardboard packaging to prevent water or other product fluids from penetrating the packaging and causing unwanted migration between the packaging and the product.Moreover, we still do not know the full extent of their impact over the long term.
“There are alternatives to petroleum-based plastics,” for waterproofing biobased packaging, says researcher, Eric Desnoes. Like PLA for example. “This material is derived from fermented corn or potatoes. Its compostability still presents a challenge under certain industrial conditions, and it’s not really recyclable due to a lack of infrastructure.” The problem with this biodegradable and compostable plastic (unlike PHA, a material currently under development that could be used to make takeaway drinks cups), is that its LCA is not ideal. We explain why below.
“ASL (Age, Sex, Location)?” In recent years, teens have been using this term in online dating. A similar question is now being asked of new materials: “LCA”, meaning Life Cycle Assessment. “We conduct a life-cycle assessment in order to calculate a material’s carbon footprint, among other things.” However, corn and potato starch are derived from “intensive monoculture farming”.
This is where the ambiguity lies with bioplastics, says Denis Paccaud, as “we must reduce the carbon emitted into the atmosphere during the manufacture and recycling processes. They are definitely not biodegradable, but if we’re not careful, they will, like petroleum-based plastics, end up adding to the “sixth continent”. The property of biodegradability is currently under debate. We don’t know whether these bioplastics will release toxic substances when they degrade, or how long it will take for their degradation to not be a risk.” As for the rest, “it’s complex; they must be biodegradable, but not for the entire duration of the packaging’s use. We don’t yet have a button that can trigger material degradation, but researchers are working on this issue.”
The molded pulp sector is a mature industry. The price is currently a barrier to market. We estimate that this type of packaging costs between 7 and 10 times more than Styrofoam.
Formerly at INRAE (the famous inventors of the tomato-based packaging), researcher Eric Desnoes now works for Innofibre, the Cellulosic Product Innovation Center. In this capacity, he is developing a form of molded pulp packaging made from cardboard, a material designed to replace Styrofoam, the fine foam used to package most of our takeaway meals. “The molded pulp sector is a mature industry. The price is currently a barrier to market. We estimate that this type of packaging costs between 7 and 10 times more than Styrofoam.”
Nonetheless, it is a promising alternative: “We are able to recycle and recover 90%. The overall average recovery rate for paper and cardboard is 70%.” The remaining 20-30% results from the afore-mentioned protective film “composed of polyethylene and aluminum” which ensures that the packaging can be fully sealed and is sterile. “70 to 80% of molded pulp, once used”.
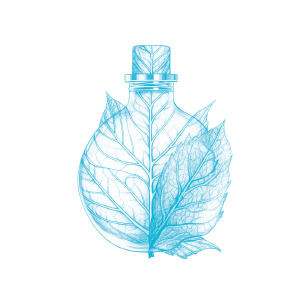
You get the picture. At present, there are no bioinspired, biobased solutions that are completely plastic free. As is often the case, the most innovative solution is still…recycling. In France, says Denis Paccaud, Carbios is working on the “enzymatic recycling” of plastics. “The system is inspired by a natural process, digestion, to put it simply. The enzyme used acts like a pair of scissors, cutting up polymers and recovering monomers so that they can be recycled.”
Could this offer a solution to recycling, as well as biodegradability, thus making plastic “fantastic” once more?
“For over 200 years, since the industrial revolution, we’ve been optimizing manufacturing processes for materials and objects, and for the last 20 years, we’ve been focused on understanding how to dismantle and disassemble them”
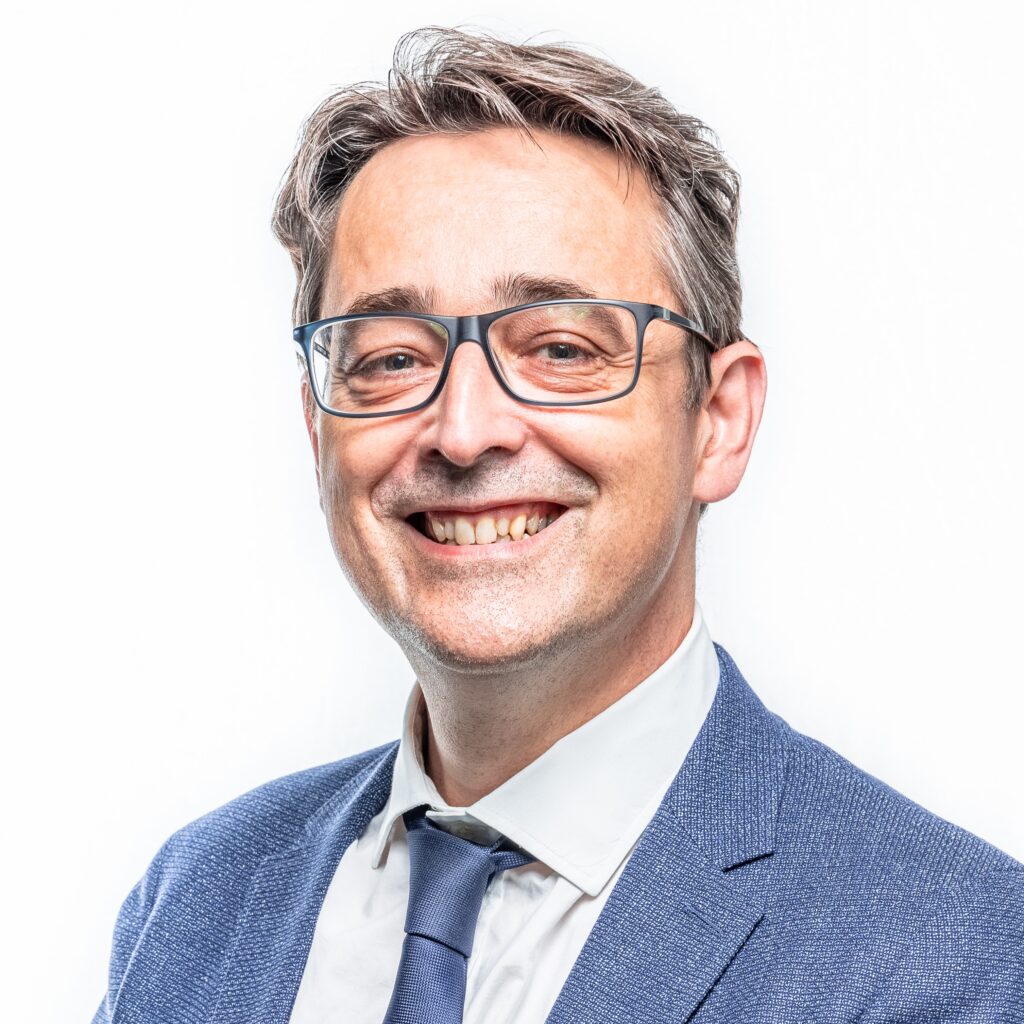
Denis Paccaud
Texen Innovation Director
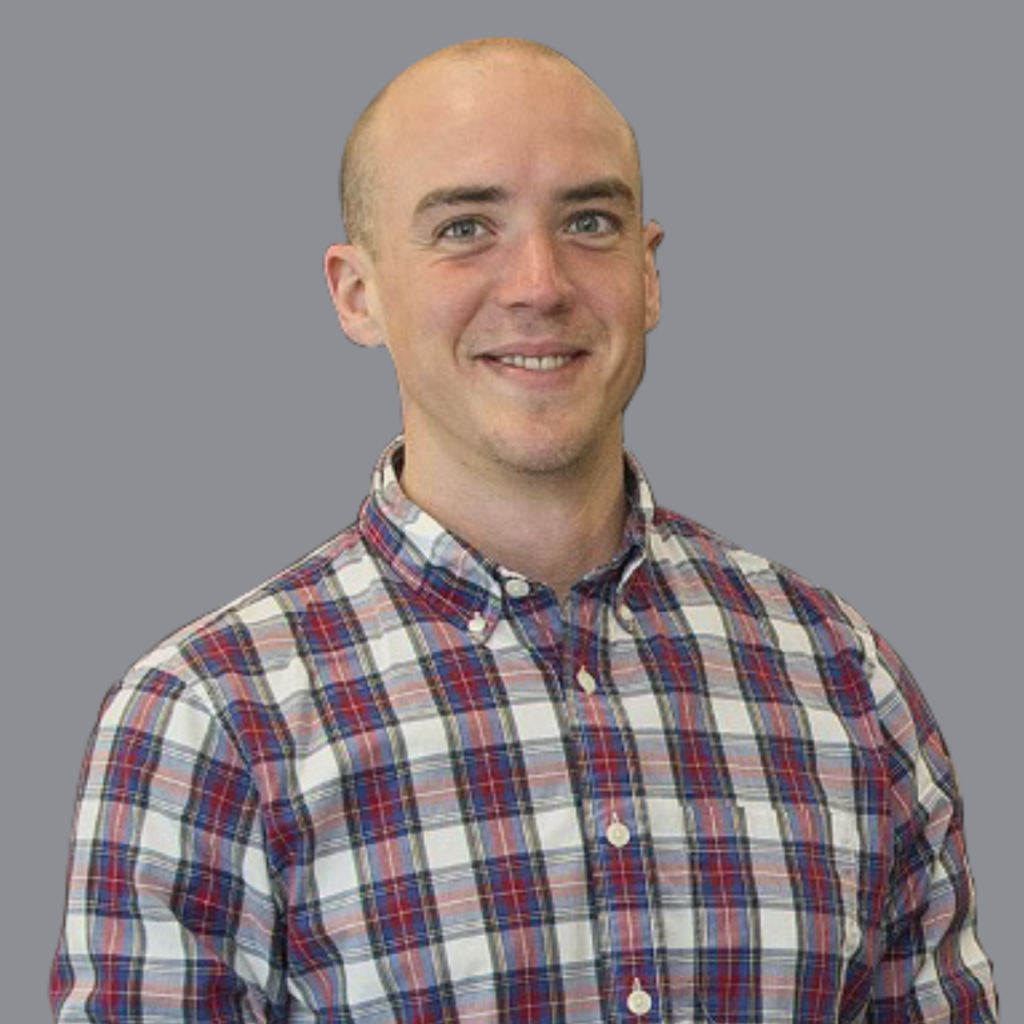